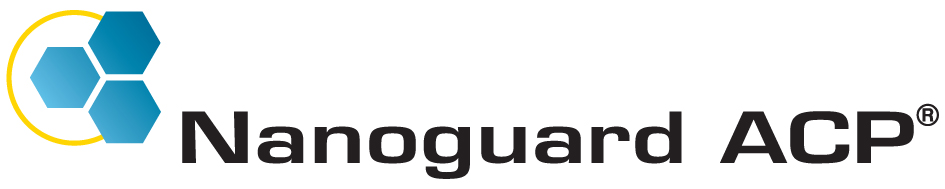
Anti-Corrosive Pigments
- Anti-corrosive pigments – used on their own, environmentally friendly
- Active constituent in anticorrosive systems designed to be safe to humans, animals and the environment, and avoid negative marketing on both consumer & industrial products
- Replacement for traditional heavy metal based ant-corrosives based on zinc, hexavalent chromium, strontium and lead
- CONEG, RoHS, FDA, Food & Potable water systems possible
- Cost effective
Corrosion testing clearly needs to show good correlation to the environment, the SSPC (Steel Structures Painting Council) tested different test methods and concluded the Salt Spray testing was a poor test method giving low correlation to actual service. The SSPC tested 15 different systems including alkyds, acrylics, epoxies and urethanes. The research compared outdoor results with results from the Combined Corrosion / Weathering Cycle, conventional salt spray (B117), a cyclic salt spray employing a 5% sodium chloride solution, Prohesion and two types of cyclic immersion test. The SSPC research has confirmed that the Combined Corrosion / Weathering Cycle provided the best agreement with severe outdoor marine exposure.
Exposure conditions include:
Electrolyte Solution 0.05% sodium chloride & 0.35% ammonium sulfate solution Acidity pH between 5.0 and 5.4
The Prohesion exposure cycle is:
- 1 hour Salt fog application at 25°C (or ambient)
- 1 hour Dry Off at 35°C (The dry-off is achieved by purging the chamber with fresh air, such that within 3/4-hour all visible droplets are dried off of the specimens.)
- Repeat